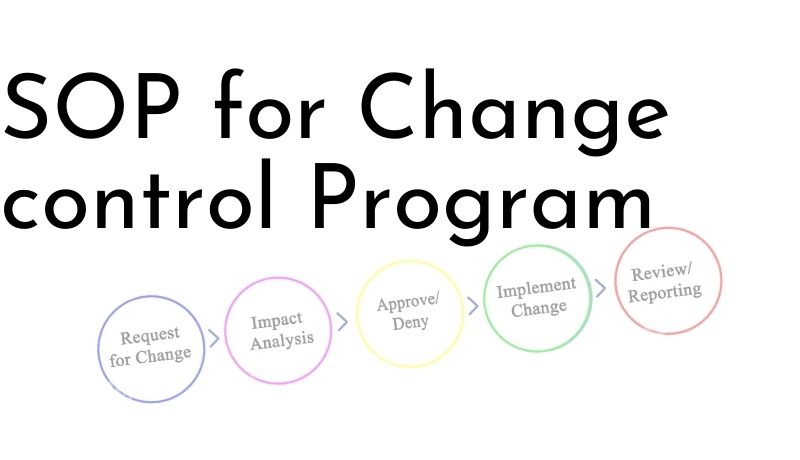
SOP for Change control Program
1.0 OBJECTIVE:
The objective of this Change control Program SOP is to provide the process for evaluation of a change against approved and or validated conditions. This evaluation must be satisfied prior to implementation of the change in GMP related aspects. This program provides a procedure to ensure that no changes are made until the requested change is reviewed, approved and deemed effective by Change Control Committee.
2.0 SCOPE:
This change control programme shall be followed whenever a change is required to be made at site, which affects strength, safety, stability, efficacy, potency, identity, purity, Quality and productivity of the drug product that shall include subsequent changes in following but not limited to:
2.1 Raw Material, intermediate and Packaging material Specification and test method.
2.2 Finished Product Specification.
2.3 Change in Raw Material in the formulation including its vendor source.
2.4 Change in Manufacturing Formula / Process including batch size.
2.5 Change in equipment / Instruments including computer hardware & software or major components of equipment / instruments.
2.6 Change in cleaning method.
2.7 Change in facilities, Locations of important processes.
2.8 Change in Bill of materials (BOM).
2.9 Change in Analytical method.
2.10 Change in Standard operating procedure (SOP).
2.11 Modification in plant, facility, manufacturing equipment / instruments and utility services.
2.12 Change in price of the product.
3.0 RESPONSIBILITY:
3.1 Change control committee consists of Head of Quality Assurance Department, respective department head requesting the change and other Heads of concerned departments, which may be affected because of the change.
3.2 Initiating Department: To initiate Change control forms (CCF) and review comments.
3.3 Head of Quality Assurance Department: To ensure compliance, Proof reading, ensure conformance to CGMP and applicability to other system, to review and approve CCF, determine regulatory impact and determine other requirements if any.
4.0 PROCEDURE
4.1 Whenever a change becomes necessary or desirable the initiator who has to propose the change shall approach Head QA / concern QA personnel for receipt of change control form (CCF) attached as respective form. The initiator shall fill a CCF describing the proposed change and the reason for change, attach supporting documents with CCF for the justification on change proposed, if any and forward to the department head by putting departmental initiation number and date on top right corner of the Annexure-I.
Department initiation Number is given as CCF001/YY
Where
001 represents the first serial number of the change control initiated by that department.
YY Year
All departments will maintain record of CCF initiation as per respective format.
Note: Changes covered by a “Change Control Form ” may include, but are not limited to the following:
– Changes requesting an additional or alternate source of raw materials.
– Changes in manufacturing procedures.
– Change in product color, shape, size and weight.
– Change in packaging and labeling.
– Changes to process and/or testing equipment.
– Changes to cGMP facility or cGMP facility utilities.
– Changes to Master Batch Production Records (Mfg. & Pkg.)
– Changes to Specifications.
– Changes to Test procedures and General test procedures.
– Changes to SOPs and equipment cleaning procedures.
– Others (as applicable) not mentioned above.
4.2 The initiator of the Change Control Form (CCF) shall mention the type of change requested, the respective document reference number if change proposed in an approved document, and briefly summarize the proposed change and reasons for change in the respective columns on the CCF and sign and date and forward to Department Head for his comments.
4.3 The Department Head shall enter his comments under the column for Department Head and forward the CCF to the Head of Quality Assurance department (change control coordinator) for his comments.
4.4 The Change Control Coordinator or concern QA personnel shall assign a number to the request and enter that number and a brief description of the proposed change with the date received into the “Change Control Register”.
4.5 The Change Control Coordinator shall forward the Change Control Form for comments of other Heads of the concerned Departments, which may be affected by the change, or may call for Change Control Committee.
4.6 On the basis of committee comments Change Control co coordinator shall evaluate the Change Control Form with respect to aspects of Validation, regulatory approval, stability studies, etc. and take decision for approving, rejecting or sending the proposal to corporate in respective change control proposal (CCP) format.
4.7 If CCP need to fill, Location QA Head or concern QA personnel fill CCP on basis of CCF.
4.8 The unique identification number to the CCP shall be as per the following pattern.
4.8.1 CCP/XXX/ 001/YY
Where,
CCP – Change control Proposal
XXX – Location Code
001- Three digits sequential number allotted to CCF by QA (Location)
YY – Year
4.8.2 The department code for CCP shall be as per respective format.
4.8.3 The QA Head / concern QA personnel shall enter the details of product/ item name Batch Number, present status, proposed changes and reason.
4.8.3 The reason shall be justified with relevant backup data / Trend analysis/ supporting documents shall be attached.
4.8.5 Head -QA (Location) shall categorize the CCP as per respective format and review the CCP with respect to:
4.8.5.1 Feasibility of change.
4.8.5.2 Impact on Quality.
4.8.5.3 Impact on Productivity.
4.8.5.4 Documents need to be amended with respect to change.
4.8.5.5 Requirement of the trials
4.8.5.6 Requirement of stability studies
4.8.5.7 Adequacy of Justification & supporting documents.
4.9 After receipt of the approved/ Rejected CCP from corporate QA, approved/ Rejected CCP shall be enclosed along with the change control form as a reference and details shall be updated in CCF.
4.10 The Change Control Coordinator/ Head QA or designee shall compile the summary of Changes whether the change request is approved or rejected in change control form in the respective columns on the basis of the comments received from corporate.
4.11 The summary compiled on the CCF shall be entered in the Change Control register and status of approved/ rejected shall be entered under the respective column whether CCF is approved/ rejected.
4.12 In case of not generating CCP, CCF will be closed locally as per procedure.
4.13 The initiating department shall be informed whether the CCF is approved or rejected, by the concern QA personnel through photocopy of approved or rejected copy shall be given by stamping “change control copy for Implementation” in green color with sign/date and “Rejected” in red color with sign/date respectively. Respective CCF No. given by QA shall be recorded and reflected on respective revised / changed document.
4.14 If the change request is Approved by the change control coordinator/ concern QA personnel and Validation / Regulatory submission / Stability testing / Training etc., required, the concern QA personnel shall coordinate with respective Head of Department to complete the same.
4.15 After fulfilling the above requirements, the Change Control Coordinator shall review the completion of the proposed change and record effective date for implementation in change control register.
4.16 The same shall be informed to the initiator and other concerned heads of departments through disposed copy of CCF.
4.17 Approved/ rejected and completed change control forms along with other supporting documents shall be filed in the “File for change control form” kept in QA Office.
4.18 Any additional changes proposed which are to be included after a CCF is approved and before changes are made effective, shall be written on the annexure for Change Control Form as per respective format.
4.19 Post implementation Review of CCF
4.19.1 If the post implementation review is required the same shall be mentioned in “Change control Form” by change control coordinator in respective column and the Review shall be done by respective/ Affected department Head as per annexure XI on due date of review. Final review shall be done by Head QA and shall be attached with original CCF.
4.20 Head – QA (Location) / concern QA personnel shall prepare the summary of change control quarterly. Refer respactive format.
4.21 Closure of CCF
4.21.1 On receipt of Approved copy of CCF initiating department head shall implement the action to be taken for compliance of requirement summarized.
4.21.2 The Change control shall be closed by the location QA by ensuring the action implemented and completed as mentioned and relevant document has been received from concerned department /agency.
4.21.3 Control shall be closed by stamping the “CLOSED” stamp on it in green color on top center of CCF and filing the same in the file. One photocopy of it shall be send to the respective department as an informative copy.
4.22 Implementation of CCP received from other location / corporate
4.22.1 Record the CCP No. and details of CCP on receipt from other than location in register as per respective format by QA.
4.22.2 Location QA head or his designee will study the impact of CCP on various systems / document of location.
4.22.3 Distribute the photocopy (in case of changes required or to be implemented) to respective department as an implementation copy as per the procedure of distribution of CCF.
4.22.4 Don’t distribute the CCP in case of no changes required. Keep the CCP as documentation / reference purpose by recording the details in respective format.
4.22.5 Respective department has to fill CCF may be for execute the change on the basis of above CCP. As a supporting document copy of CCP attached to CCF.
4.22.6 Follow the procedure applicable for CCF.
4.22.7 Update the details of implementation in register as per respective format.
5.0 ANNEXURE (S):
Annexure – I: Change control form (CCF)
Annexure – II: Change control register.
Annexure – III: List of Department codes
Annexure – IV: Change control proposal CCP
Annexure – V: Annexure to change control form
Annexure – VI: Categorization of minor and major
Annexure – VII: Format for Summary of change control
Annexure – VIII: Flow chart for change control form
Annexure – IX: Departmental change initiation record
Annexure – X: Record of CCP received other than location
Annexure – XI: Post implementation review of CCF
Annexure- I: Change control form (CCF)
CCF No.:
Initiated by:
Department:
Date :
Type of Change Requested
Master BMR
Master BPR
Manufacturing process
Packaging
Labeling
Utility
Specifications
Standard Test Procedure
GTP
SOP
Cleaning procedure
Equipment
Others
Document No. _______________
Title :
Proposed change (Attach the annexure / supporting documents if any ) :
Reasons for change (Attach the annexure / supporting documents if any):
Date:
Sign of Initiator:
COMMENTS WITH SIGNATURE AND DATE :
Department Head:
Head Quality Assurance:
Other Department Heads:
Summary of Change Control Committee comments:
1) Validation required? Yes/No
2) Stability required? Yes/No
3) Training required? Yes/No
4) Regulatory Submission : Required / Not required
5) Others :
Change Request: APPROVED / REJECTED
Change Control Coordinator (Sign/Date):
Validation Completed (if applicable)
Signature:
Date:
Stability Completed (if applicable)
Signature:
Date:
Regulatory Approval Obtained (if applicable)
Signature:
Date:
Document Revision completed (If applicable)
Signature:
Date:
Training completed (if applicable)
Signature:
Date:
Others
Signature:
Date:
Change Request Reviewed:
Effective Date:
Closing Remarks:
Change Control Coordinator (Sign.) :
Date:
Post implementation review require
Yes/No
Annexure- II: CHANGE CONTROL REGISTER
S No.
Change Request Notice Number
Initiator Dept / Area
Proposed change
Remarks about proposed change
Approved/ Rejected
Effective date of change
Annexure- III: LIST OF DEPARTMENT CODES
Department -Department code
Quality Assurance – QAD
Quality Control – QCD
Microbiology – MCD
Production – PRD
Personnel and Administration – HRD
Warehouse (RM/PM/BSR Store) – WHD
Engineering – END
Annexure-V Annexure to Change Control Form
CCF No.: _____________
Document reference no:_______________
Point Number
Existing point/System
Proposed Change
Reason for change
Requested by/Date
Checked by/Date
Approved by/Date
Annexure – VI: Categorization of Major and Minor Changes
MINOR: Changes, which can be noted and corrected at scheduled program. Example:
i) Manufacturing
1. Similar change part equipment changes
2. Change in coating Lots.
3. Change in vendor non-critical excipients.
4. Change in location of equipment from one area to other.
5. Change in Batch size using equipment operating on similar principle.
6. Change in manufacturing site within the same building using equipment operating an Similar principle.
ii) Documentation
7. Specification changes for amendment of units.
8. Change in specification status
9. Merging of similar product codes in TMD/ TAD.
10. Change in secondary packaging components
MAJOR: Which directly or indirectly affects the quality, safety, and purity of product which is a not complying GMP practice. Corrective action to be taken immediately.
iii) Specification
11. Relaxing an Acceptance Criteria or deleting a test for raw material that: Raw Material or finished Product.
12. Change in pharmacopoeia, compendial requirement, changes in the TAD to meet the validation status without changes in the quality attributes.
Categorization of Major and Minor Changes
13. Improvement in critical quality attributes (specification).
14. Relaxing the acceptance Criteria
15. Deletion addition of any part of the specification.
16. Change in TAD used for testing
17. Revision of TAD as per current Pharmacopoeias.
18. Revision in specification of critical Parameter.
iv) Manufacturing
19. Change in manufacturing site for final drug product to: different location.
20. Change in process/or process parameter.
21. Improvement in process capability, efficiency.
22. Improvement in yield.
23. Change in process of manufacturing affecting the impurity profile / or the physical, chemical, or biological properties.
24. Changes related to the starting material all stages.
25. Change in Batch size (If not using equipment with similar operating principle)
26. Change in packaging Mode.
27. Change in equipment, which is significantly different from the previous equipment even there is no modification to the process Parameter.
v) Shelf Life.
28. Extension of an expiry date.
29. Extension of expiry date based on new / revised stability or on full time shelf life data.
Annexure – VII: Format for Summary of change control
Sr. No.
CCF
No
CCP No
Corporate CCP
Dept.
CCP Details
Product / Material
Code / Batch No./ Sop No.
Strength
Category
Type/Nature
Date of Initiation
Date of Approval
Sent to Corporate
Approved CCP received on
Action to be taken
TCD
Effective Date
Closure status
Annexure- IX: Department change initiation record
Sr.No.
Department Initiation No. & Date
Initiated
By
Details of change proposed
Approved / Rejected
Sign. for closure.
Annexure- X: Details of CCP received from other than Location
Sr. No.
Date of receipt
CCP No.
Change suggested
Affected Department / Document
Implementation copy issued to Department
Received by.
CCF No. for Implementation
Closing Date of CCF
Comments (if any)
Annexure- XI – Post implementation review of CCF
CCF No.:
Review Due Date:
Department:
Brief description of change made
Review comments of initiating Department Head
Sign:
Date:
Review comments of other affected Department Head:
Comments of Head QA
Sign:
Date: